The competition in the industrial world requires one to constantly come out with the newer, the better, and the more efficient technology which solves the problems of various production processes. Moreover, new materials are being worked with in various production processes, which one would have never imagined could be used for that purpose. In order to put such materials in various applications different methodologies are required.
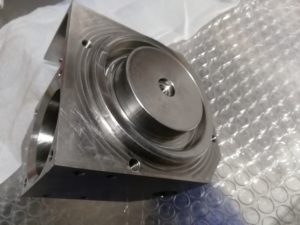
REQUIREMENTS FOR MACHINING HARD STEEL
Hard materials like S7 steel and H13 steel are many a times required in molds due to their remarkable properties like impact resistance and temperature resistance. Although these hard materials improve the performance of the final products, but these materials require tough machinability. Machining hard materials seem almost impossible for many manufacturers. For machining hard materials one requires – A rigid tool system of high precision, tough and hard tool material, tool holders of high stiffness, proper and appropriate tool geometry and cutting conditions, etc. There is a huge difference in the machining process of hard materials and normal materials used for making molds. Working with hard steels requires the application of the right tools, right strategy and the right technology at right production stages.
TOOLS FOR MACHINING HARD STEEL
The right tools are required by productionists to machine hard steels. Working with hard steels requires one to have all the tool parameters accurately and precisely calculated. It is a must to consider well the sharpness and the edge measurements of the tool.
Square end, ball end and bull nose mills are used at different production stages. The mill with ball end does roughing and finishing operations. The mill with bull nose end is operated on large and flat surfaces. This tool is not so perfect as it gives rise to chipping. The corner parts of the material are processed by the mill with square end. These tools should be occasionally oiled and dry machining should be done with air to maintain their optimum performance.
RIGHT STRATEGIES
Working with hard materials requires the application of right strategy too. For instance, these days hard turning of the parts is done prior to the grinding to the final finish. Grinding process is specifically expensive and needs to be done in accordance with different shapes of materials. Now manufacturers are using various strategies to easily and swiftly turn a prehardened part. Insert selection plays an exceedingly important role in the process of hard turning. Selection of suitable insert is complementary to the process. For materials with much higher ranges of hardness, CBN inserts are used. Wear and tear of tools will necessarily require its maintenance like sharpening and hence the edges of the tool are varied. This variation needs to be accounted in the CAM programming. The best strategy used is the elimination of sharp turns and rather introducing small arcs at the corners in the program. This helps in the machining of corner parts and avoids the wear and tear of the machine. A sudden change of direction by 90 degrees slows down the machine.
RESOURCE BOX
Klarm is one of the leading CNC machining shop in china. Different types of processes like CNC Milling China are employed in production of various goods. Contact us to get good milling services and quality machined parts.
The original source of this article is from http://www.cncmachinings.com.