Today, the metal fabrication industry uses a lot of processes and milling is one of them. Milling allows tradesmen to cut and shape rolled steel. In the machining field, milling centers are of many types, but two types are quite common. They are known as horizontal machining and vertical machining. In this article, we are going to take a look at vertical machining and the way it works in the machining field.
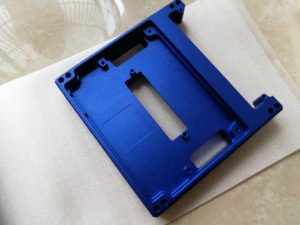
Vertical milling involves cutting elements, aka spindles. They have vertical alignment. Unlike vertical mills, horizontal ones are parallel to the ground. Both the machines do the same job, but the production methods are a bit different.
Vertical machining is also known as milling. It depends on rotary cutters for the removal of metal. It occurs on a VMC that uses a spindle that has a vertical orientation. This type of machine is operated with the help of a computer. Examples of these machines include laser cutting, water-jets, routers, EDM machine and so on.
How a Vertical Milling Machine Works
Generally, the term” vertical indicates the orientation of the cutting tool or spindle. The spindle is also called the cutting head. The position of the cutting head is fixed but some parts do move on different axes.
As far as the types of vertical mills are concerned, most industries use two types: bed and turret. Each has its own set of benefits. Let’s discuss both of the types.
Turret Mill: This type features a spindle that doesn’t change its location. But the bed part that holds the stuff does change its location on a vertical or horizontal level. This is the reason a turret mill is known as a versatile mill. However, it’s important to keep in mind that these mills are good for small pieces alone.
Bed mill: in a med mill, the material moves horizontally. The spindle moves along the vertical axis as per the need. The spindle movement and the bed movement allows the milling of different types of depths and shapes. So, a bed mill is a great choice for those projects that require large or heavy pieces.
Benefits of vertical milling
Most of the machinery you can find in different industries fall under the category of vertical machining. They cost of this machinery is low compared to the horizontal milling, which makes them a good investment choice.
Typically, their low upfront costs allow a business owner to offer products at a lower price. Moreover, finding operators for this type of machinery is not hard.
Easy operation: the structural design of the VMC allows greater visibility. So, the operators find it easier to identify and fix the problems the machine is working. Moreover, the user-friendly controls make it easier to do the programming as well, which means that the operators can perform the setup quickly.
The great level of visibility makes it easier for the operators to complete big projects. Since they are easy to use, simple jobs are even easier to complete. If you need fast milling jobs, you can go for these machines.
So, this was an introduction to the vertical milling and the way it’s used in the machining field.
CNC machining companies in China can provide you with quality CNC machines for the growth of your business.
Resource box: This article is originally posted in http://www.cncmachinings.com.